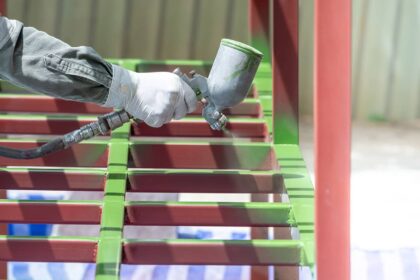
We can define a coating as a liquid, liquefiable, or mastic (thick film) composition that, after application to a surface, is converted into a solid, protective, decorative, or functional adherent film.
If you are new to the coatings industry, you may be asking what is the difference between paint and coating. While the two terms are often used interchangeably, they are actually different materials. Simply put, paint is for aesthetic or decorative purposes, and coatings are applied for performance or protective purposes.
While there may be some protective qualities that come with painting anything, that is not the real purpose of paint. Coatings are paints with purpose. The word coating generally describes a material, thicker than paint, which has a more functional purpose. In an industrial environment, that function is primarily to protect the metal substrate against the effects of corrosion.
The primary use of coatings is to provide corrosion protection, but there are numerous other reasons for the application of protective coatings, they are: aesthetics, performance requirements, safety identification, and most importantly, corrosion prevention and control.
Aesthetics
One of the primary reasons why coatings are applied is aesthetics. While it might seem odd to focus on aesthetics when talking about industrial applications, appearances still matter. Coatings can contribute to a positive first impression and help consumers make choices. We all know that consumers choose items to purchase based on their design and visual appeal just as much as their functionality.Coatings also help consumers make choices by increasing the appeal of a product. Coatings can also be used to attract consumers with appealing colors or use color to signify a brand such as Coca-Cola red or Facebook Blue. In addition, coatings contribute to the impression of cleanliness and can appeal to the consumer’s interest in owning the product and pride in ownership. You may have heard the saying, “you never get a second chance to make a first impression,” and part of that first impression is due to appearance. In short, coatings can help build or destroy credibility in a product, a company, or the associated people in just one look.
Performance Requirements
Industrial coatings perform a wide variety of different functions that are based primarily on the location of the structure, severity of exposure, the length of service life desired, and long-term corrosion protection.Another reason why coatings are commonly applied is to enhance the performance of the object being coated. Coatings can be formulated to meet specific needs, such as enhancing the function or durability of the substrate. As an example, a coating can be used to increase friction on stairs and walkways to prevent slips and falls. Shown below are some of the desired properties a coating may be formulated to meet. When formulating coatings, there is usually a trade-off made among the properties as no one coating can contain all of these properties.
- Chemical Resistance: The coating must resist breakdown from the chemicals to which it is exposed.
Chemical resistance is primarily a function of the resin used.
- Water Resistance: Water affects virtually all coatings. Greater water resistance equates to more effective
corrosion control. It can be used to prevent or reduce the transmission of liquid or moisture or reduce the
transmission of water vapor.
- Ease of Application: Ease of application is a vital characteristic, especially with intricate structural details.
The more difficult the application, the more opportunity for defects to be created, leading to premature
failure.
- Adhesion to Substrate: Adhesion is based on physical and chemical interactions between the coating
and the substrate. Poor adhesion equates to poor performance.
- Cohesive Strength: Coatings must be able to withstand the stresses of the curing process and changes in
temperature and moisture content.
- Flexibility and Elongation: The ability to expand and contract with the substrate is critical in some
coating applications.
- Impact Resistance: The coating may have to resist impact loads.
- Biocides: Resist attack by fungus, insects, rot, and mildew on wood and cementitious surfaces.
- Decontamination: Provide easier decontamination or cleaning of substrates.
- Abrasion Resistance: Reduce wear on the substrate from abrasion.
- Temperature Resistance: The environment may expose the coating to extreme hot or cold
temperatures.
- Marine Fouling: Antifouling or foul release coatings keep marine surfaces smooth and reduce drag, as
well as the attachment of marine organisms to the hulls of ships and other submerged structures.
- Weatherproofing: Protection against degradation from the environment; wind-driven debris and/or
erosion, water, temperature fluctuations, ultraviolet sunlight, etc.
- Luminescence: Allow signs to be seen in the dark or in areas that could lose lighting.
- Passive Fire Protection: Fire retardant coatings are applied to resist the spread of fire.
Safety Identification
Coatings are commonly applied to enhance the safety of an environment. Safety identification refers to signs and markings that provide viewers with information, directions, and guidelines. These markings can inform an individual of correct and appropriate actions after just one glance.
Coatings can also be applied to provide more general guidance, such as directions to a particular location or correct procedure when parking. Within industrial environments, however, the items that are typically coated include the identification of safety-related items such as walkways, pipe identification, and other items that require color-coding due to government regulations. Other examples of how coatings are used as safety or process identification include:
- Belt guard to provide safety protection from the motor of an air blower.
- The contents of vessels and pipelines, such as yellow to represent flammable gas and blue to represent water.
- Safety guidance, like clearly marking designated walkways and hazardous areas.
- The correct procedure, as an example, what waste items to place in each bin or container.
- Directions, for instance, a colored line at an airport that guides passengers to their destination.
Corrosion Prevention and Control (CPC)
Protective coatings are the most common and extensively used corrosion protection system. In industrial environments, asset owners deal with corrosion by establishing and maintaining corrosion prevention and control (CPC) programs. The purpose of CPC is to prevent the start of or reduce corrosion through the use of coatings, cathodic protection,alteration of environment, materials section, design,and inhibitors, as well as through proper inspection and maintenance practices throughout the life cycle of the asset.Coatings are the most widely used method for controlling and preventing corrosion. Approximately 90% of all expenditures associated with corrosion control are related to protective coatings.
The Growing Cost and Impact of Corrosion
Corrosion is not only dangerous; it is also an extremely costly problem that impacts nearly every industry. In 2016, NACE International published the International Measures of Prevention, Application,and Economics of Corrosion Technologies study,otherwise known as the IMPACT study. The study found that the global cost of corrosion is an estimated $2.5 trillion (USD) per year, which is the equivalent of 3.4% of global Gross Domestic Productor GDP. The indirect cost of corrosion is estimated to be at least equal to the direct cost. (E.g., lost,productivity, taxes, overhead costs, etc.) It is estimated that up to 30% of annual corrosion costs can be saved if corrosion management practices were employed.At home, corrosion can consume your cookware, your children’s playground equipment, or even your outdoor furniture, gardening tools, or barbeque set. Within industrial settings the consequences can be disastrous. Corrosion can cause buildings to collapse, pipelines to rupture, ships to sink, and chemical plants to leak.